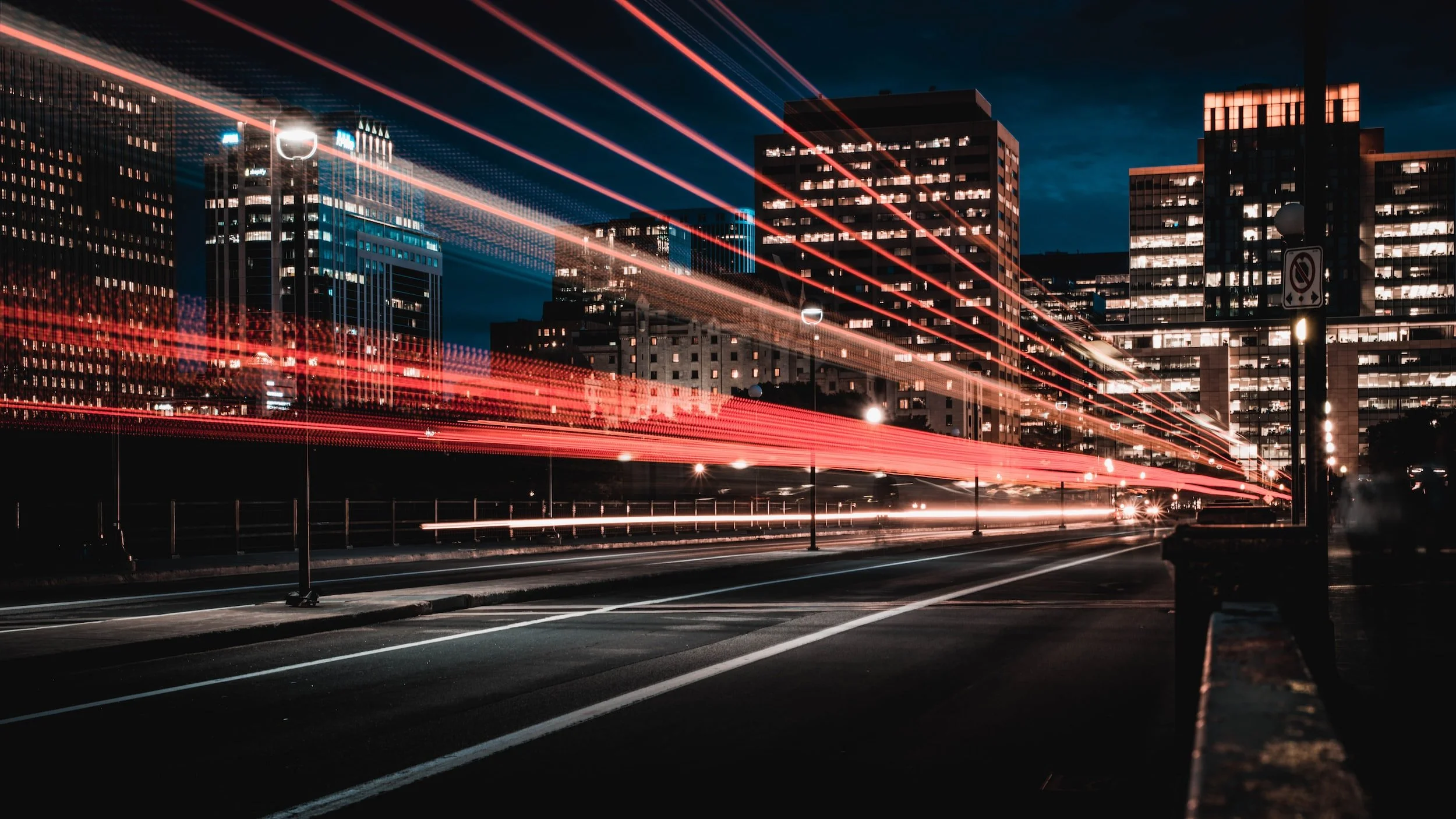
THE SILVER LINING BLOG
The Latest & GREATEST
Quality Matters: Inside Silver Lining Collision’s Success Strategy
Top priorities, when it comes to car repairs, are safety, quality, and efficiency . In order to consistently meet these standards Silver Lining Collision has adopted the 5S system.
The 5S system is a methodology developed in Toyota’s production system by Tahichi Ohno during the 1960’s in Japan and over time has been influenced by various manufacturing principles and Japanese management practices.
At Silver Lining Collision quality is more than just a philosophy; It’s ingrained into our very culture through what we call the ‘Right Now Mentality.’ The ‘Right Now Mentality’ is a guiding principle that emphasizes the importance of quality in all aspects of our work and empowers our employees to be vigilant, proactive, and engaged in delivering the best possible service to our customers.
Quality is a shared Goal
In our facility, quality is a shared goal that every employee takes ownership of. Every team member, from our office manager to our technicians, is given the autonomy to halt production whenever they detect a potential quality issue or lack of excellence in the output. We believe that each employee’s perspective and input are invaluable in upholding our commitment to delivering top-notch services.
Our Employee’s Voices Matter
We foster an environment where feedback is welcomed and received with enthusiasm and attention. By actively listening to our employees and creating a culture of open communication we ensure that their concerns are addressed promptly, guaranteeing that our quality promise to our customers remains unwavering.
The 5S system is a methodology developed in Toyota’s production system by Tahichi Ohno during the 1960’s in Japan and over time has been influenced by various manufacturing principles and Japanese management practices.
Quality Right the First Time
Our goal is to make sure that we get the quality right the first time. Though this may require additional efforts and resources, we prioritize fixing any issues immediately, even if it means foregoing short-term gains. Our commitment to first-time quality sets the foundation for building trust with our customers, assuring you that your vehicle will be restored to the highest standard with no return visits necessary.
Putting Our Mentality into Practice
An incident with a customer’s car serves as a prime example of how our ‘Right Now Mentality’ comes to life. While replacing a woman’s bumper damaged in an accident, our meticulous quality check revealed damage to the fender and under the bumper. Without hesitation, our attentive technician used his walkie-talking to signal the problem. We promptly gathered to assess the situation, discussed the best approach forward, and proceeded to fix the additional damage, even though it was unrated to the initial accident. This proactive approach exemplifies our dedication to delivering excellence at every turn.
At Silver Lining Collision, the ‘Right Now Mentality’ is not just a catchphrase; it’s a way of life that defines our culture and drives us to provide exceptional service to our customers. By empowering our employees to take charge of the quality and actively participate in the process, we ensure that every vehicle that comes through our doors receives nothing but the best. Our relentless pursuit of excellence is what sets us apart, and we will continue to live by this guiding principle, always striving to exceed expectations and bring satisfaction to those we serve.
Embracing a Customer Service-Centric Culture at Silver Lining Collision
At Silver Lining Collision (SLC), we believe that great customer service is the cornerstone of our success. As a premier brand based in Dallas, Texas, we are dedicated to restoring the pride and confidence of Texas drivers. Let’s chat about the amazing company culture that has made us a sought-after workplace for those seeking a fulfilling career in the collision repair industry.
At Silver Lining Collision (SLC), we believe that great customer service is the cornerstone of our success. As a premier brand based in Dallas, Texas, we are dedicated to restoring the pride and confidence of Texas drivers. Let’s chat about the amazing company culture that has made us a sought-after workplace for those seeking a fulfilling career in the collision repair industry.
State-of-the-Art Facility and Employee Training:
One of the foundations of our company is our state-of-the-art indoor collision repair facility. With a meticulously thought-out floor plan, equipped with cutting-edge machinery, our facility is designed to ensure maximum efficiency and productivity. Our commitment to providing the best customer service experience begins with comprehensive employee training. We invest in our staff, equipping them with the necessary skills and tools to deliver exceptional service to every client.
Customer and Employee Focus:
At SLC, we firmly believe that decisions should always focus on the best interests of our customers and employees, instead of short-term financial goals. This philosophy guides our actions and ensures that we consistently deliver on our mission. By putting the needs of our customers and employees first, we cultivate an environment where everyone can thrive and grow.
Implementing the 5S System:
To maintain a streamlined workflow, we follow a strict 5S system. Our commitment to support and training ensures that all employees follow the 5S principles: Sort, Straighten, Shine, Standardize, and Sustain. Each team member plays an important role in contributing to our overall productivity and success. This system encourages collaboration, enhances efficiency, and ensures a seamless repair process every time.
Empowering a 'Right Now Mentality':
We empower our employees to take ownership and accountability for their work. This means that when a problem arises, our employees are encouraged to halt their tasks, identify the root cause of the issue, and find immediate solutions. By fostering a problem-solving culture, we ensure that our customers receive top-notch service at every step of the repair process.
Open-Door Policy and Employee Support:
At SLC, we value open communication and prioritize the well-being of our staff. Our open-door policy encourages employees to approach management at any time, for any reason. We believe in empathy and provide a supportive environment where team members can freely express their thoughts and concerns. By fostering a sense of camaraderie and support, we create a workplace where everyone feels valued and empowered.
Leadership Development and Teaching Philosophy:
We are committed to developing our employees into leaders who embody our philosophy. Through comprehensive training and hands-on experience, our staff members gain a deep understanding of our work and values. This mindset ensures that our employees become ambassadors of our brand and principles.
Giving Back to the Community:
At SLC, we understand the importance of community involvement. As we prosper, we aim to give back to our community through both our business practices and philanthropy. We have a strong passion for supporting our veterans and the wider community, and we look forward to making a positive impact as we continue to grow.
Silver Lining Collision has cultivated a company culture that focuses on customer service. Through our commitment to employee training, state-of-the-art facilities, and a focus on the well-being of our team, we have created an atmosphere where employees thrive and customers receive exceptional service. As we continue to expand, we are determined to uphold our values and make a positive impact on our community.
Dealing with Hail Damage? Here's What You Need to Know
If you've been hit by a hailstorm, we understand how frustrating it can be to deal with the aftermath. Dents and damage can suddenly appear, causing stress and inconvenience in your busy life…
If you've been hit by a hailstorm, we understand how frustrating it can be to deal with the aftermath. Dents and damage can suddenly appear, causing stress and inconvenience in your busy life. The first step to take is to file a claim with your insurance company. However, we know that this can be a time-consuming process, and you may not want to take time out of your schedule to deal with it. It's important to know that you don't need to file right away. Keep in mind that if the storm just came through, the claims department may be operating with a skeleton crew, and there will be a lot of people calling in. You have up to two years from the time of the hailstorm to file your claim, so there is no need to worry about doing it immediately.
At Silver Lining Collision we specialize in Paintless Dent Repair (PDR) and offer a thorough triage process. The first step is to bring your car to our shop and let us take care of the rest. We'll wash your car and circle up the dents, then get it under the lights to determine the best course of action. Our expert technicians will assess the damage and decide which panels need PDR, conventional repair, or replacement. Once you’ve initiated the claims process with that initial phone call, we'll handle everything else on the back end, including writing the estimate and making sure the insurance company pays us in full. You'll only owe your deductible, and we'll take care of the rest.
Paintless Dent Repair (PDR) is a highly effective and efficient way to fix hail damage. It's the most affordable option and leaves the car's original paint and factory clear coat undamaged. Unlike conventional repairs, PDR doesn't require filing or sanding down the affected area, resulting in a faster and more cost-effective repair. At our collision repair shop, we call upon our team of PDR specialists who are dedicated to this process. They use various methods to remove the dents, including working from the inside with precision or using glue pull techniques from the outside.
There are several methods of Paintless Dent Repair (PDR) that can be used in a collision repair facility, including:
Pushing from the backside: This involves massaging the dent out from behind the panel using specialized tools. It's a popular technique for small to medium-sized dents.
Glue pulling: This method involves attaching a plastic tab or a metal device to the outside of the panel, then using hot glue to pull the dent out from the front. It's typically used for larger dents.
Blending: This technique involves smoothing out the dent by gently tapping the area around it to blend the metal back into shape.
Heat shrinking: This is a specialized PDR technique that involves using a heat gun to shrink the metal around the dent, allowing the technician to manipulate the metal back into place.
Specialized tools: PDR technicians use a variety of specialized tools to manipulate the metal back into shape, including hammers, picks, and rods.
The specific method used will depend on the size, location, and severity of the dent. If a dent cannot be fixed with PDR, we carefully evaluate the damage to determine the next steps. Our collision repair facility will first consider whether the damage can be repaired using conventional repair methods. This may involve using body filler or metal glaze to fill in the dent and then repainting the affected area. However, if the damage is too extensive or there are multiple spots on a panel, it may be more cost-effective to replace the panel entirely, especially if it's a bolt-on panel.
Replacing a welded panel can be more labor-intensive, and the collision repair facility may face supply chain issues if it is after a major hailstorm. In such cases, we may opt to spend more time having the PDR specialist focus on areas where PDR can be effective to ensure that the damage is fixed properly. Our goal is always to provide the most efficient and cost-effective solution to get your car back on the road as quickly and safely as possible.
At Silver Lining Collision, we're committed to providing excellent customer service and educating our clients. If you have any questions about hail damage or need to schedule an appointment, please don't hesitate to reach out to us.
Maximizing Customer Satisfaction: How the 5S System Benefits You
Top priorities, when it comes to car repairs, are safety, quality, and efficiency . In order to consistently meet these standards Silver Lining Collision has adopted the 5S system.
The 5S system is a methodology developed in Toyota’s production system by Tahichi Ohno during the 1960’s in Japan and over time has been influenced by various manufacturing principles and Japanese management practices.
Top priorities, when it comes to car repairs, are safety, quality, and efficiency . In order to consistently meet these standards Silver Lining Collision has adopted the 5S system.
The 5S system is a methodology developed in Toyota’s production system by Tahichi Ohno during the 1960’s in Japan and over time has been influenced by various manufacturing principles and Japanese management practices.
The five S’s stand for sort, straighten, shine, standardize, and sustain and are meant to promote efficiency, organization and cleanliness in the workplace.
Sorting is the act of separating necessary tools from the unnecessary items to reduce clutter and make it easier for technicians to find what they need quickly. This leads to faster repairs and less downtime for the customer.
Straightening is arranging the necessary tools and equipment in a way that promotes efficiency allowing the technicians to work more quickly and accurately leading to quality repairs and fewer mistakes.
Shine involves cleaning the workspace to maintain a pristine environment to prevent accidents and injuries while promoting a more professional and welcoming atmosphere for customers.
Standardizing and establishing procedures ensures consistent results and reduces the likelihood of errors which leads to higher quality repairs and fewer return visits from the customer.
Sustain involves continuously maintaining and improving the system to lead to even greater efficiency, quality, and safety in the facility. This helps the repair center to stay ahead of the changing technologies and best practices in the industry.
This system not only keeps our employees safe and efficient but also benefits you, our customer. Faster repairs means less downtime and a faster return to your daily routine. This system allows us to continuously produce high quality repairs giving you the peace of mind that there will be no future issues with your repaired vehicle. The 5S’s increase the safety of our environment for employees and customers alike, reducing the likelihood of accidents or injuries.
Every day our techs start by removing and storing away unnecessary items in their tool boxes. Socket sets, ratchets, wrenches, pliers, screwdrivers and other necessary tools are arranged on their individual carts that stay within reaching distance to the technician throughout the repair process. This organization and storage helps techs locate tools quickly and reduce the risk of misplacing them. Our technicians clean their tools and our porters maintain our facility daily. Our SOPs (Standard Operating Procedures) are reviewed and updated each year to ensure we are performing and producing at the highest quality standards.
As someone who cares about their safety and vehicle you should make sure the collision repair center of your choice follows a system like the five S’s. This might not always be readily apparent but here are a few ways you can draw a conclusion as to if they are implementing such a system. Simply look around the repair center and see if the workspace is organized and tidy. Is there clutter anywhere? Ask the center how long it typically takes to complete repairs such as yours. If the center follows a five S system, they should be able to give you a clear and efficient timeline for repairs if they have already given you an initial estimate or consultation. You can also ask directly if your repair center follows the 5S system or a similar procedure.
Overall, by choosing a center like Silver Lining Collison you can expect fast, high quality repairs in a safer and more welcoming environment.
A SILVER LINING: OUR FACILITY + EQUIPMENT WERE BUILT AND PURCHASED WITH INTENTION
When it comes to choosing a collision center to repair your vehicle, there are many factors to consider. While price and convenience may be the first things that come to mind, it is important to also take into account the quality of the facility and equipment that the center uses.
One question you may ask is,
"Why did you build your facility this way?”
The answer is simple: a high-quality indoor facility and equipment, like that at Silver Lining Collision, can make a big difference in the quality of the repair work. With 45 years of combined experience in the industry we knew what we wanted from the paint booth down to the footprint and air flow in our facility.
We have invested in a top-of-the-line paint booth from ACCUDRAFT: a booth designed to provide the perfect conditions for a flawless paint job, ensuring that your vehicle looks as good as new when you get it back.
Another essential piece of equipment we use at Silver Lining Collision is our Spanesi Bench with Spanesi Touch 3D measuring. The Spanesi bench is an advanced vehicle repair system designed to restore damaged cars and trucks to their original factory specifications. The bench is constructed of heavy-duty steel and features multiple anchoring points for securely holding the vehicle in place during repairs. The Spanesi Touch 3D measuring system is an advanced measuring tool that allows technicians to quickly and accurately assess the damage to a vehicle and create a 3D model of the repairs needed. The system uses high-resolution cameras and laser sensors to scan the vehicle and create a detailed digital model of its structure. When used together, the Spanesi bench and Touch 3D measuring system create a powerful combination that helps technicians achieve precise repairs with a high level of efficiency. The Touch 3D measuring system provides the technician with real-time measurements and comparisons to the vehicle's original specifications, ensuring that the repairs are accurate and the final result is up to industry standards.
Another piece of high-quality equipment we’re proud to use is our GYS PTI-Genius welder: a versatile machine that can be used for a range of welding applications, including spot welding, MIG welding, and brazing. One of the key features of the PTI-Genius welder is its advanced technology that allows for precise and efficient welding. The machine uses a pulse technology that enables the user to adjust the pulse time and energy level, resulting in a precise and consistent weld. All of these tools and equipment are necessary for fixing cars quickly and correctly, exactly how they were from the manufacturer.
Our footprint is set up to maximize service in the least amount of time getting you back on the road quickly. The proper airflow within our indoor facility ensures, not only that employees are safe but that your car is repaired in a controlled environment where outside particles do not pose a hazard to the outcome of your repairs.
While investing in high-quality equipment and an indoor facility, Silver Lining is sure to provide their customers with a level of service that is hard to beat.
When choosing a collision center, it is important to look beyond just the price and convenience. Take the time to research the facility and equipment that the center uses. Look for a center, like ours, that has invested in the latest and greatest equipment, such as a top-of-the-line paint booth and frame machine. By doing so, you can ensure that your vehicle is repaired correctly and safely, and looks as good as new when you get it back.
So, don't hesitate to ask questions like "Why did you build your facility this way?" or "What type of equipment do you use?"
You'll be glad you did.